OMRON Motion & Drives
Motion Controllers
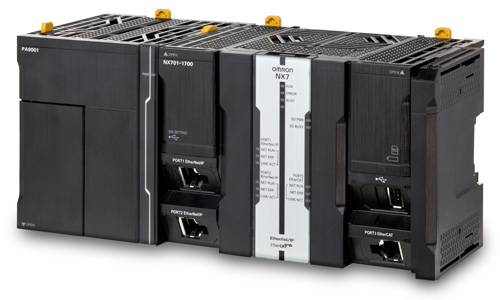
NX7 series
The NX7 series is a high performance machine controller that includes two synchronized motion cores controlling up to 256 axes.
- Fastest cycle time: 125 μs
- Number of axes: 256, 128
- Two synchronized motion cores
- Functions: Logic sequence and Motion
- Multi-tasking
- Built-in EtherCAT and two EtherNet/IP (1 Gbps) ports
- Fully conforms to IEC 61131-3 standards
- Certified PLCopen function blocks for motion control
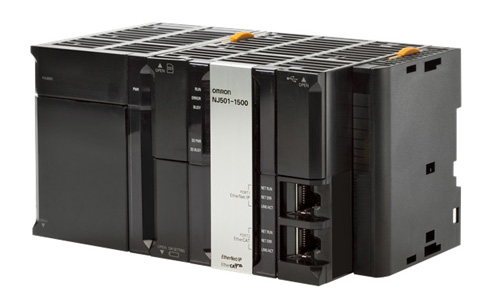
NJ series
The NJ series is an scalable machine controller for logic sequence and motion control that includes options for advanced functions such as robotics and database connection.
- Fastest cycle time: 500 ms
- Number of axes: 64, 32, 16, 8, 4, 2, 0
- Synchronized motion core
- Functions: Logic sequence, Motion, Robotics, Database connection and SECS/GEM
- Up to 8 Delta robot control
- DB connection: SQL client for Microsoft SQL server, Oracle, IBM DB2, MySQL, Firebird
- Multi-tasking
- Built-in EtherCAT and EtherNet/IP ports
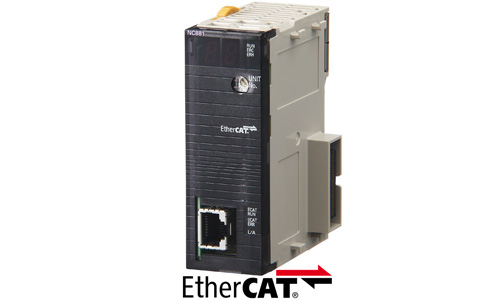
NC EtherCAT
In the minimum of space you can have a complete and powerful position control system when combining the Omron CJ2 PLC, the CJ1W-NC EtherCAT unit and the G5 servo drives with EtherCAT built-in.
- Position control units with 2, 4, 8 or 16 axes
- NC_82 models support up to 64 additional nodes: inverters, vision systems and distributed I/Os
- Linear and circular interpolation
- Linear and infinite axes management
- Programming languages: ladder and function blocks
- Certified PLCopen motion control function blocks
- The unit can perform various operation sequences in the memory, operation data
- CX-Programmer software for unit setup, EtherCAT network configuration and PLC programming
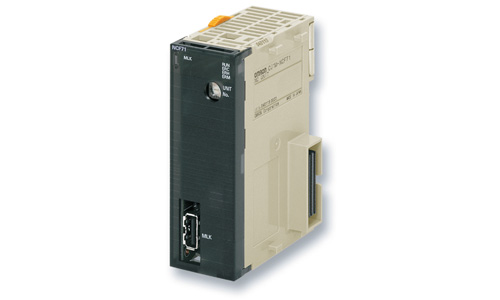
NC MECHATROLINK-II
NC MECHATROLINK-II is a powerful controller for point-to-point applications. It is based on MECHATROLINK-II Motion Bus, which reduces programming and development and maintenance costs. Supports PLC Open Function Blocks.
- Position control units with 2, 4 or 16 axes
- Simplified wiring (I/Os). Data routing to all servo drives (MECHATROLINK-II)
- Integration into Omron Smart Platform: Function Blocks, Smart Active Parts, CX-One
- Servo drives’ full control and parameter access via Mechatrolink
- Supports position, speed and torque control
- Easy, fast, reliable, optimised for positioning applications
- Advanced PTP: 8-axis (4 Dim.+ 4 Dim.) interpolator
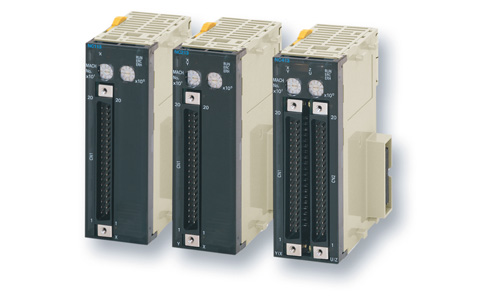
NC Analogue Output
The NC motion controllers support positioning control via pulse-train outputs. Positioning is performed using trapezoidal or S-curve acceleration and deceleration. Ideal for controlling simple positioning in stepper motors and servos with pulse-train input.
- Positioning can be done by direct ladder commands
- Position and speed control
- Linear interpolation
- Interrupt feeding function
- Positioning of 100 points done from memory
- Positioning data is saved in internal flash memory, eliminating the need to maintain a backup battery.
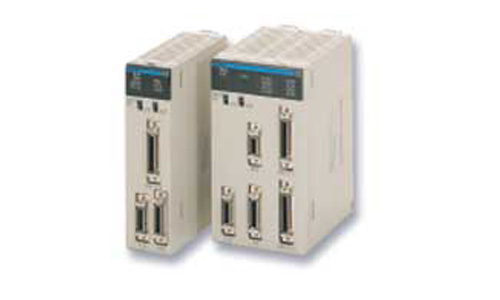
MC Analogue output
The MC module provides closed-loop control via analogue outputs for up to 4 axes and supports G-Language for advanced, high-speed, high-precision position control. Several modules can be supported per PLC CPU.
- Up to 4 axes with one unit and 76 axes per PLC CPU
- Winding operations are easily controlled with traverse positioning
- G-code programming
- Multi-tasking
- Linear, arc and helical interpolation
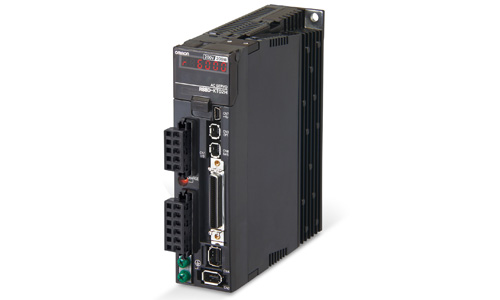
G5 Servo
The Accurax G5 Analogue/ Pulse series is supplied with an integrated positioner as standard. This positioner capability is provided to the user via a Drive Programming environment, and is ideal for simple positioning applications like assembly machines, sorting and pick and place projects. The Drive Programming functionality is included in the standard CX Drive configuration tool.
- Drive Programming: internal positioning with indexer functionality
- Basic positioning functions
- Position operations: up to 32 points
- Frequency response of 2kHz
- Safety conforming to ISO13849-1 (PLd)
- High accuracy provided by 20 bit encoder
- Advanced vibration suppression
- Full closed loop encoder built-in
- Rotary motors from 50 W up to 15 kW
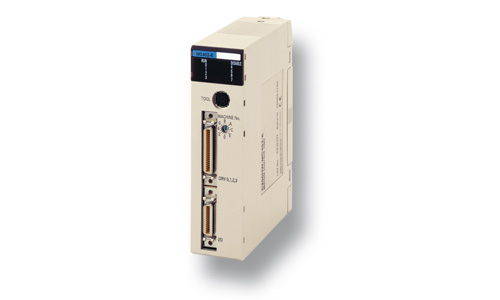
MC402 Analogue output
The MC402 is a PLC-based advanced motion controller. It controls 4 axes and up to 16 modules can be installed in the same PLC. The module controls the position speed or torque of the servo drive via an analogue output. This PLC-based condition opens the controller to the whole system.
- Simple programming
- Powerful motion commands
- Multiple controllers in CPU
- Registration input for every axis
- True multi-tasking
Servo Systems
Servo Drives
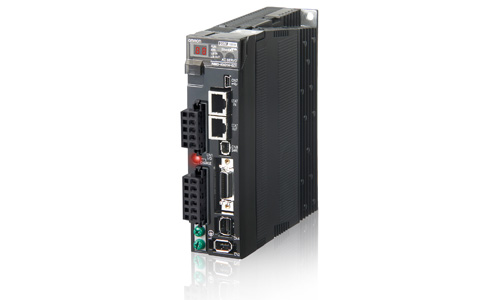
G5
Accurax G5 gives you that extra edge to build faster, accurate, smaller and safer machines. You will gain almost 25% in motor weight reduction and 50% cabinet space saving. You will achieve sub micron precision and ms settling time.
- EtherCAT, MECHATROLINK-II and Analogue/Pulse drive models
- Frequency response of 2kHz
- Safety conforming to ISO13849-1 (PL d)
- High accuracy provided by 20 bit encoder
- Drive Programming: embedded indexer functionality in the Analogue/Pulse models
- Advanced vibration suppression
- Full closed loop encoder built-in
- Double registration input provides application versatility
- Rotary motors from 50 W up to 15 kW
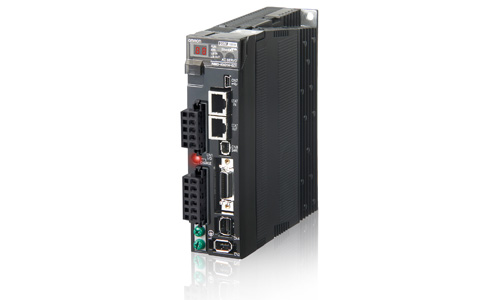
1S
The 1S is a general purpose servo motor.
- 23-bit resolution encoder
- Fast and secure screw-less push-in in all connectors
- Pluggable connectors for easy pre-wiring and system maintenance
- Direct wiring of I/O signals
- Embedded relay for direct motor brake control
- Improved loop control for overshoot and quick setting time
- Safety function built-in:
- Network Safe Torque Off: PLd (EN ISO 13849-1), SIL2 (IEC 61508)
- Hardwired Safe Torque Off: PLe (EN ISO 13849-1), SIL3 (IEC 61508)
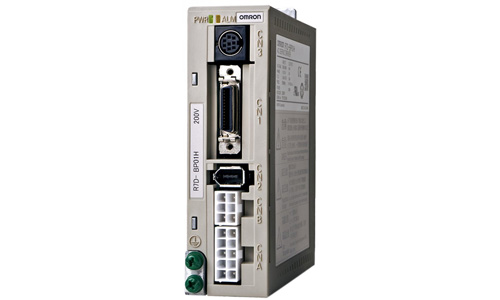
R7 (SmartStep 2)
The new SmartStep offers an ideal solution for point-to-point motion applications where simplicity is essential. SmartStep 2 keeps things simple whilst combining high performance and advanced features in a cost effective solution.
- Ultra-compact size. The footprint is only 48% compared to the previous SmartStep
- Vibration suppression
- Adaptive resonance suppression filter
- Feedback pulse output
- On-line Auto-tuning and Easy set up
- Electronic gear, four internal speed settings and wide range of pulse settings
- Two torque limits
- Position control via pulse input 500 kpps
- Configuration and commissioning using CX-Drive software
Servo Motors
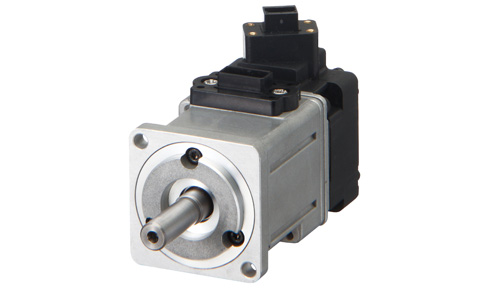
G5
Accurax G5 servomotors include IP67 protection and connectors on the motor body. Use of 10 pole motors and 20 bit encoder results in 40% reduction in motor cogging. The servomotors are 25% lighter and 15% smaller due to patented new stator design PAC-Clamp, 40% iron loss reduction and 15% smaller encoder.
- Sizes from 50W to 15 kW, rated speeds of 1000 rpm, 1500 rpm, 2000 rpm and 3000 rpm
- Peak torque 300% of continuous torque during 3 seconds or more depending on model
- High accuracy provided by a 20 bit resolution encoder, ABS encoder as an option
- IP67 protection in all motor models
- Low speed ripple and low torque ripple due to low torque cogging
- Compact design and robust construction including smart connectors
- No motor settings required, just plug and run
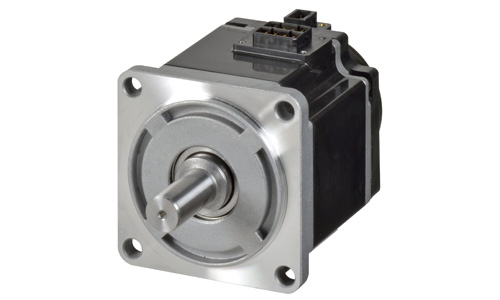
1S
Simplified machine design and maintenance.
- 23-bit resolution encoder
- Compact and small motor size
- Multi-turn encoder design without mechanics: 16-bit, 65536 turns
- Battery-free absolute multi-turn encoder
- Pre-assembled motor cables
- Designed for easy EMC compliance
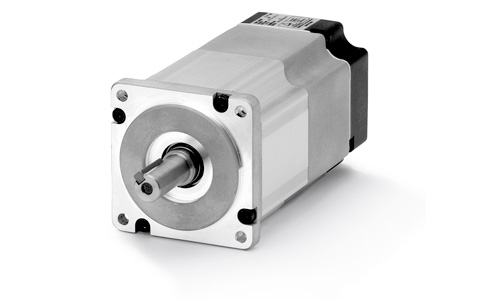
R7 (SmartStep 2)
A wide range of compact servomotors to meet all application needs. When used with a SmartStep 2 drive, the G-series servo motors offer the simplicity and cost-effectiveness of a stepper with the added advantages of a servo system.
- Sizes from 50 W to 1.5 kW, rated speed 3,000 rpm
- Peak torque 300% of continuous torque during 3 seconds or more depending on model
- Servomotors supported by SmartStep 2, G-Series and Accurax G5 servo drives
- Encoder accuracy of 10000 steps/rev as standard and 17 bits-INC/ABS as optional
- Cylindrical and Flat servomotor types are available
- IP65 as standard and shaft oil seal available
- Motors with brake as an option
- No motor settings required, just plug and run
Linear Motors
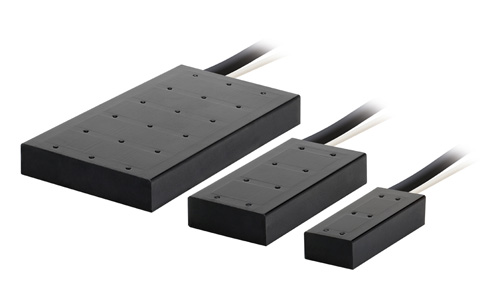
Linear FW
Iron-core motors for high speed and high duty cycle operations. This motor family delivers unparalleled accuracy and performance benefits.
- High dynamic and precise positioning
- Compact and flat design iron-core motors
- Weight-optimized magnet track
- Optional digital hall-sensor and connectors
- Temperature sensors included
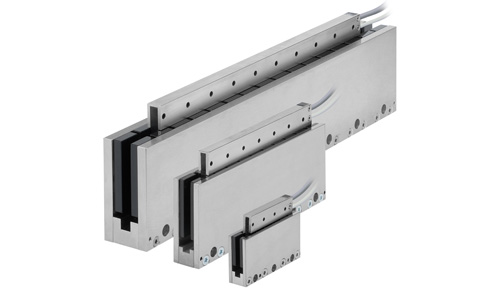
1S
Ironless motors for cog-free and high dynamic applications. This motor family deliver unparalleled accuracy and performance benefits.
- High dynamic and precise positioning
- Excellent force-to-weight ratio
- Weight-optimized magnet track
- Optional digital hall-sensor and connectors
- Temperature sensors included
Frequency Inverters | AC Drives
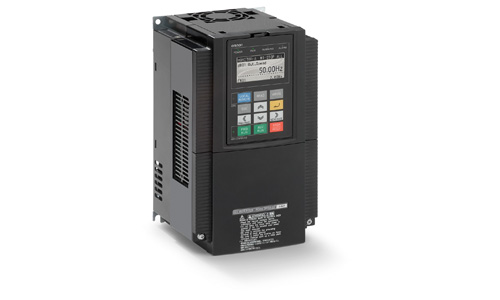
RX
We realise that you need quality and reliability, plus the ability to easily and quickly customise your inverter to the application in hand. And with the RX, you have the perfect tool for the job. Naturally it combines the same high level of quality and performance for which Omron is renowned. It also has abundant application functionality on board and can be customised to match your precise requirements.
- Up to 132 kW
- High starting torque in open loop: 200% at 0.3 Hz
- Full torque at 0 Hz in closed loop
- Sensor-less and vector closed-loop control
- Double rating VT 120%/1 min and CT 150%/1 min
- Built-in EMC filter
- Built-in logic programmability
- Built-in application functionality
- Positioning functionality
- Automatic energy saving
- Micro-surge voltage supression
- Fieldbus communications: Modbus, DeviceNet, Profibus, Componet, EtherCAT and ML2
- CE, cULus, RoHS
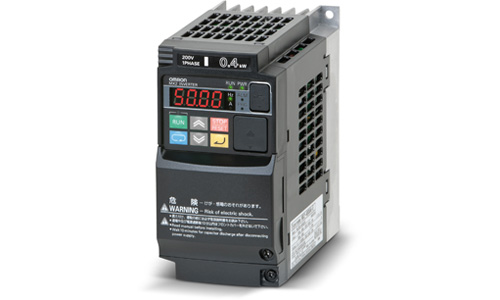
MX2-V1
Specifically created for your application, the MX2 was developed to harmonise advanced motor and machine control. Thanks to its advanced design and algorithms, the MX2 provides smooth control down to zero speed, plus precise operation for cyclic operations and torque control capability in open loop. By using the standard MX2 series functionality and communication option boards, the MX2 IP54 is the perfect choice for your standalone inverter solutions.
- Up to 15 kW
- 200% starting torque
- Torque control in open loop
- Double rating VT 120%/1 min and CT 150%/1 min
- IM & PM motor control
- Safety conforming to ISO13849-1 Category3 performance level PLD
- Built-in Logic programming
- Positioning functionality
- Integrated at Omron machine Automation solution
- Fieldbus communications: EtherCAT, Modbus, DeviceNet, Profibus, CompoNet, MECHATROLINK-II and EtherNet/IP